Automated Slot die high-precision slit coating
adjustable ipad stand, tablet stand holders.
Automated Slot die high-precision slit coating solution
Brand: DATAMAKER Model: DT-3030
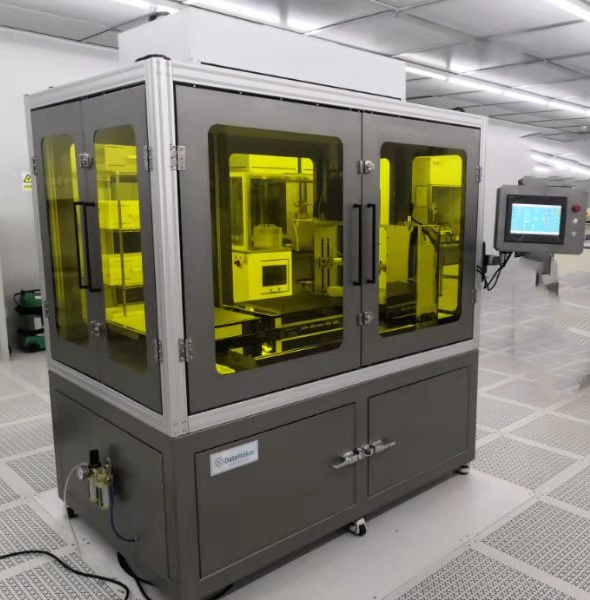
Introduction to Process and Application
1. The coating system mainly includes a feeding unit and a coating unit. The coating unit is composed of upper and lower molds made by precision machining and thin gaskets installed between the upper and lower molds. The feeding unit consists of injection pumps and filtering devices for storing and transporting materials. The system consists of a coating mold that moves precisely relative to the substrate. By controlling the speed, precise metering, and pumping of the process fluid, the liquid chemical material is extruded from the gap between the upper and lower molds and coated onto a moving substrate (glass, stainless steel, plastic, etc.) to form a thin film. The thickness of the coating can be directly calculated from the liquid flow rate and substrate movement speed, which has the advantages of high coating uniformity, wide range of applicable coating viscosity, fast coating speed, and the ability to produce large-area coatings.
2. Suitable for coating substrates such as organic solar cells (OPV) and perovskite solar cells (PVK), non continuous substrates such as LCD glass substrates for photoresist coating, as well as optical films (such as brightening films, Hardcoats, polarizing films, diffusion films, etc.), OLED coatings, etc.
3. Multiple specifications and sizes are available for customization, and a variety of user-friendly configurations are available: heating table, special gas blowing system, multi size cutting head, multi specification gasket, etc., to meet customers' various needs and tailor high-precision professional equipment for customers.
2.1 Whole machine design scheme
Introduction to Process and Application
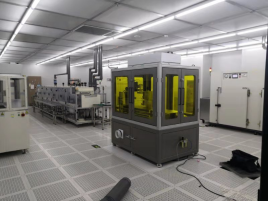
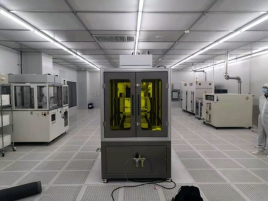
(Physical picture of slit coating machine)
2.1.1 The overall equipment adopts a two-stage adjustment to ensure the levelness of the large-area platform. The coating platform has a separate leveling mechanism, and whether the platform is flat is the first step of the process threshold, which is equivalent to the foundation.
2.1.2 The entire coating platform bottom adopts a high-precision marble platform, which is less affected by thermal expansion and contraction, and has high horizontal stability.
If equipped with in-situ heating function, the sample stage of the coating system will be designed with high-precision stainless steel. If there is no in-situ heating function, the sample stage of the coating system adopts a high-precision marble platform, which also has sample positioning and sample stage horizontal adjustment functions to ensure flatness.
2.1.4 The coating blade is made of specially designed precipitation hardened stainless steel and imported large-sized blade with special surface heat treatment (proprietary patented design technology), which is resistant to organic solvents and deformation.
2.1.5 The blade head is equipped with a 316 stainless steel gasket to adjust the gap between the upper and lower lip openings of the coating to determine the liquid output.
2.1.6 The Z-axis adopts a servo motor combined with an encoder and a grating ruler double closed loop to ensure the positional accuracy and levelness of the tool head.
2.1.7 Integrated injection pump, capable of linked control of solution flow rate, automatic liquid inlet, automatic degassing, and automatic pipeline cleaning (requires cleaning solution, and the cutting head needs to be disassembled for cleaning).
The operating mechanism of the coating platform adopts a linear servo motor to improve the stability of the platform and minimize the factors affecting the process to the extreme.
2.1.9 Waste liquid recovery system, which can be used in conjunction with pipeline cleaning for waste liquid recovery, facilitating waste liquid treatment.
2.1.10 The coating platform is equipped with multi zone vacuum adsorption function and substrate positioning function, which facilitates substrate positioning and fixation during the coating process.
2.1.11 Multi stage coating process ensures better control of the film thickness at the beginning and end of the substrate.
2.1.12 Compressed air enters the high-pressure chamber of the air knife, and the airflow flows out from the gap in the length direction of the air knife, forming a thin high-strength air curtain.
2.2 Software Functions
2.2.1 System parameter visualization, directly displaying platform position, blade height, slit thickness, coating speed, injection speed, injection volume and other parameters, combined with formula storage function to achieve good process repeatability.
2.2.2 It can be equipped with customized coating process control, such as heating table temperature control, special gas blowing switch and other functions.
2.2.3 With formula storage function, it can save more than 8 sets of mature process parameters, achieving good process repeatability.
2.2.4 It is equipped with automatic safety protection function, which uses feedback from multiple sensors equipped with it to automatically identify dangerous areas and ensure the safety of the coating mold from hitting the knife during operation.
Process indicators
Slit coating machine host | The entire coating host includes: vacuum adsorption, contact points Tool alignment device, blade head, gasket |
Distance between mold head and platform | Fine tuning adjustable range: 0-10mm Unit adjustment accuracy: 0.001mm Coarse adjustable range: 0-50mm |
Substrate | Rigid substrate/flexible substrate | Syringe capacity | 25ml |
substrate thickness | 0.05-10mm | Automatic mode extraction quantity | 0.1-25m |
Coating platform area | 300mm*400mm | Blade height | 20-1000um |
Width of coating head | 300mm | Blade levelness | ±3um |
Dry film thickness of coating | 0.05-20um | Platform flatness | ±3um |
Viscosity | 0-20000cps | supply voltage | 3φAC380V、50HZ、5KW |
Solid Content | 1-75% | Blade slit width | 0.05/0.08/0.1mm(determined by the thickness of the gasket) |
coating speed | 0.002-200mm/s | Fixed base station | by suction |
Discharge speed | 1-100mL/min | Base station configuration | In situ heating function, air knife, filter, automatic cleaning device FFU |